PMC
We built a software that helps them to plan production efficiently
Client overview
PMC by Pomemet is the manufacturer of high-quality accessories for different heavy machineries from energy woord grapple’s, quick couplers,sweepers to digging buckets and much more. Each piece is carefully designed to complement the equipment it is used on, whether it is a catalog or a custom-order product. From their Estonian-based factory, products are exported mainly to Baltic and Scandinavian markets. For a company who makes such unique products a custom production management system (PMS) was required.
What we did
Prior to working with Thorgate, an accounting software for inventory management and paper-based work orders for production were used to manage the processes. Due to that, the same information was being replicated to multiple locations. In order to reduce the overall management workload and provide a better insight into actual production efficiency, a custom software was developed that integrated directly into the accounting system. In addition to that, it allowed each order to be tracked from it being created, all the way through different steps of production, welding, finishing all the way to assembly and a Waybill or a CMR being created within the system.
The software itself consisted of 4 parts: Orders, Production planning and Production and Reports. In the orders view, all the relevant details about the order can be seen such as the client details, products but also the necessary components required to produce this.

In the Production planning phase, the user can see similar orders from the past, to add as a reference for the workers, assign the stages the product needs to pass as well as edit the component list required for this order or even add or create additional products, if need be.
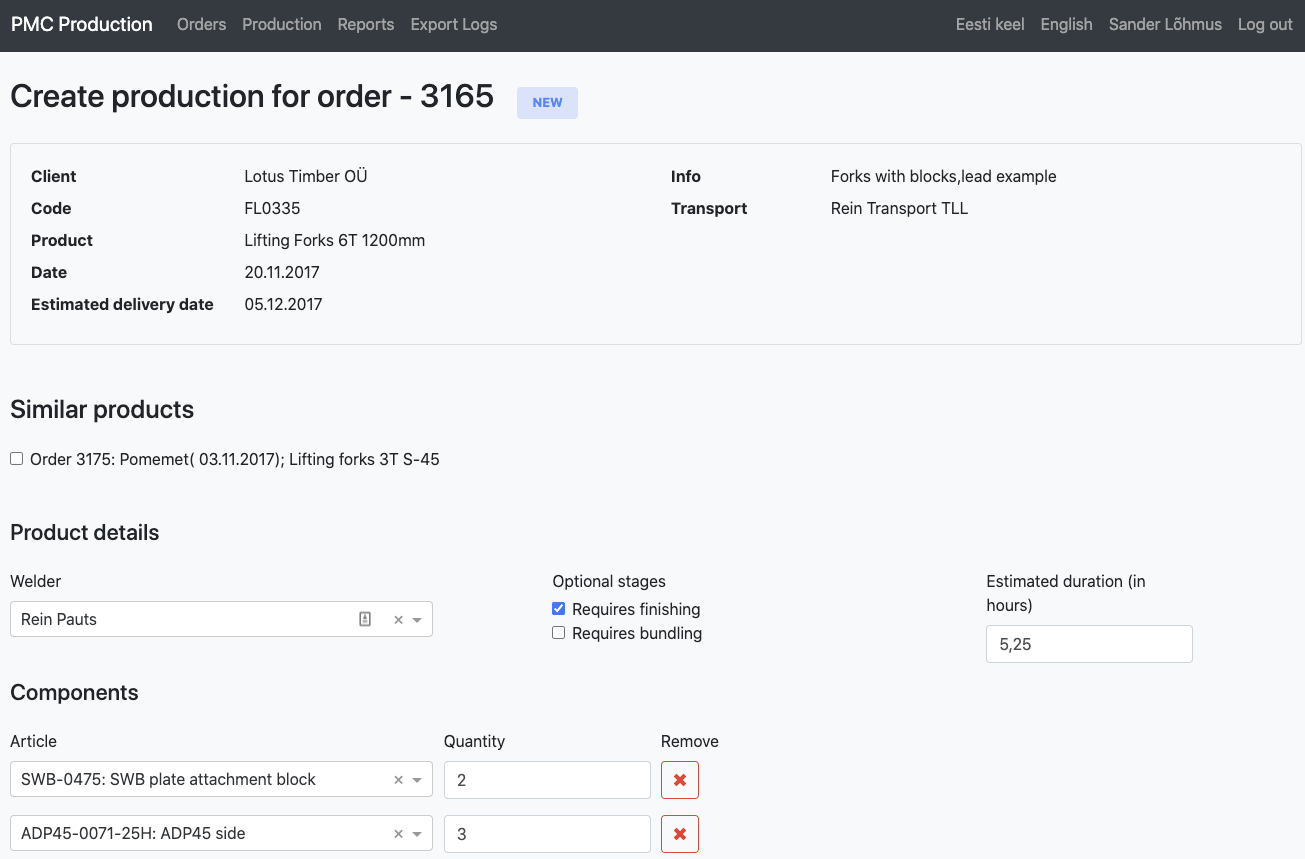
Once the order has been sent to production, the workers themselves can see the works assigned to them from their Tablets and logg time under each product separately pressing play or pause whenever they are working or 1 or another order/product, or even cancelling it with an X when something went wrong and marking it as done ✓ once they are finished. Cancelling or finishing the product makes it disappear from the workers view as they are no longer relevant for that employee at that time.
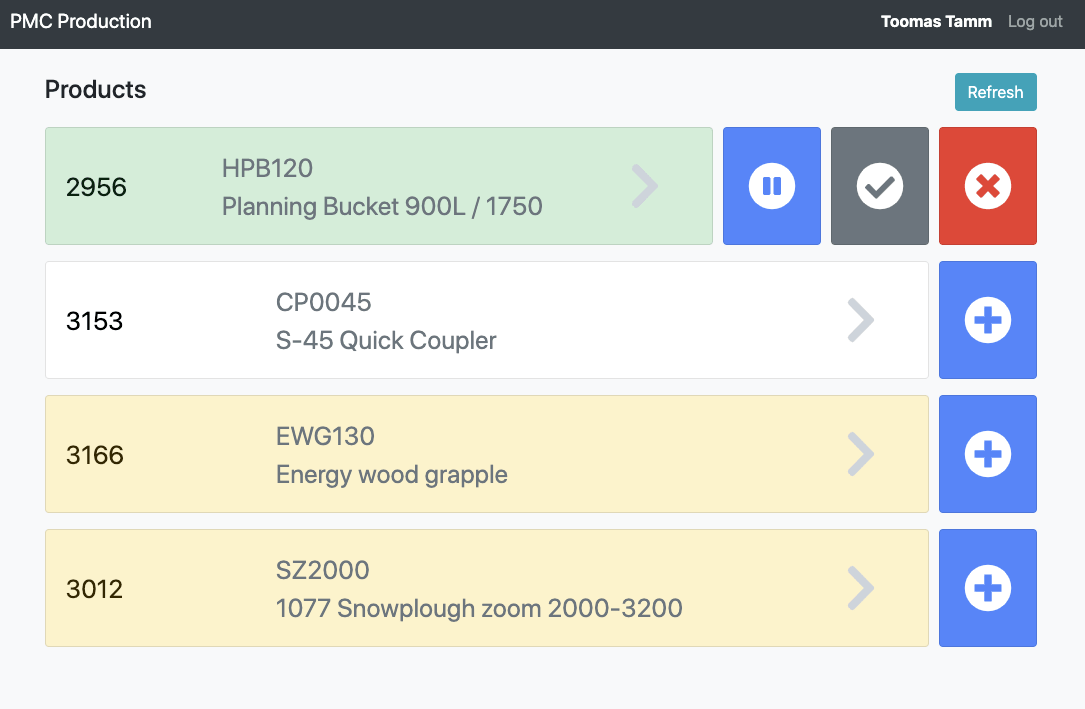
The worker can also open each product and see additional details that might help them work on this order as well as feedback from quality control in case the product came back from QA.

Scalable Technology
We used Python, and Django framework in the backend and Bootstrap and React for Front-End, making use of Celery for asynchronous tasks allowing us to thus leverage existing know-how to reduce the product turnout time.
The Success
Thanks to the created system the company gained greater insight into actual time spent per product, average turnaround time as well as the types and regularity of mistakes that had occurred in the production over a period of time, allowing them to gear their focus more on creating value to their customers rather than day-to-day administration. Since the system is also integrated with accounting then all the details regarding any order can be neatly found in a single place. For instance, the time to create the CMR for full truck load of goods decreased from half an hour to 10 minutes. Also tracking of the products across the shop floor is much quicker, no need to go to the shop floor to check the progress of the product but it’s possible to check it from my mobile. Meaning no necessary calls and wasted time. Also quite many customers use their Portal to check ordered products and their statuses.
Thorgate project managers understood how we work very quickly
- Sander Lõhmus, COO of Pomemet OÜ